MOULDEX VS THE REST
WE'RE NOT LYING WHEN WE SAY THE BEST PERFORMING MOULDINGS ON THE MARKET.
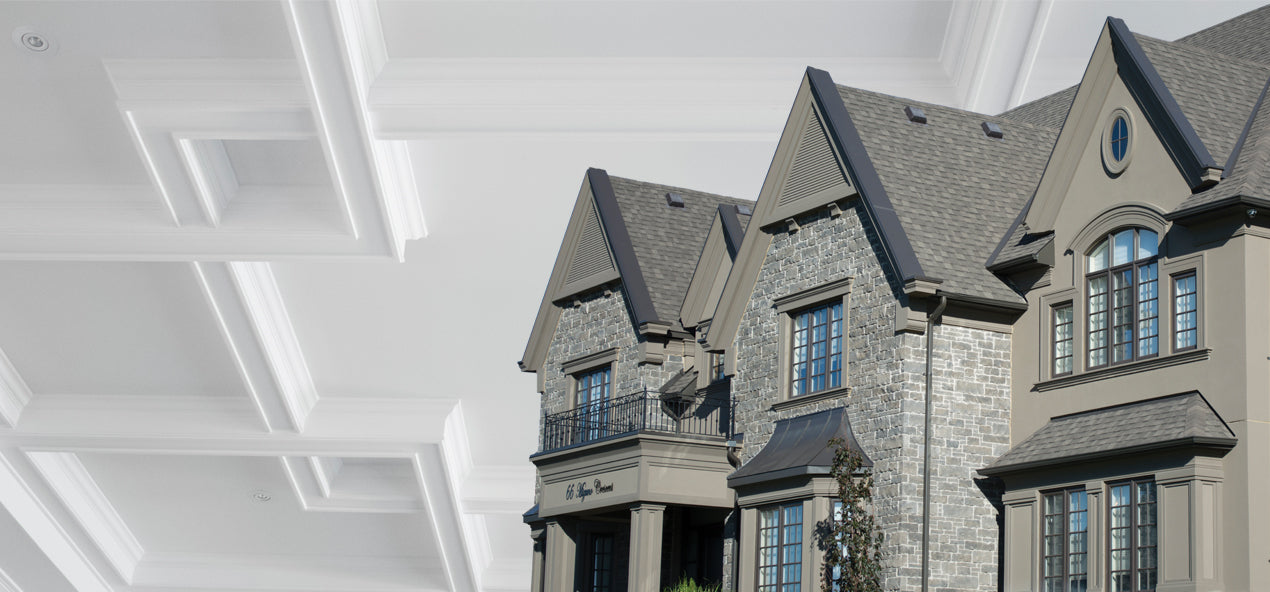
SAFER THAN POLYEURETHANE
Polyurethane mouldings are often chosen for their flexibility and ease of installation, but their use comes with significant health and environmental concerns.
HARMFUL FUMES
Using polyurethane indoors can expose you to fumes with a number of potential side effects. These fumes can lead to:
- Irritation of the eyes, throat, and lungs: This can cause discomfort and long-term health issues.
- Severe allergic reactions: Individuals with chemical sensitivities may experience heightened allergic responses, leading to more serious health concerns.
Decision makers who choose not to use polyurethane often look for safer and more sustainable alternatives.
Mouldex Mouldings have become a viable alternative, eliminating the problems commonly associated with polyurethane versions.
SUPERIOR TO WOOD
While wood continues to be a popular material of choice for exterior architectural details, its vulnerabilities present a big question mark in terms of its longevity and sustainability.
From the very moment that a coat of paint is applied over wood, its ability to breathe is blocked. Being an organic species, this will eventually lead to various issues from constant maintenance, rotting, warping and splitting to name a few.
Decision makers who choose not to use wood typically look at composite products or inorganic solutions.
Mouldex Mouldings have become a viable alternative, erasing the problems normally associated with wood versions.
INORGANIC IS BETTER.
Our exterior composite mouldings are manufactured using completely inorganic raw materials. This means that they do not need to breathe in order to maintain their appearance. This also makes them more resistant to water, fungi and insects.
WHO HAS TIME FOR MAINTENANCE?
Mouldex Mouldings are virtually maintenance free. While wood generally needs to be scraped and re-finished every couple of years, our products are able to hold up exceptionally well. The only consideration of re-painting would be when you decide to change your exterior colour scheme.
COME IN ONE PIECE. STAY AS ONE PIECE.
Achieving a detailed profile in wood as one piece is difficult. More often than not, pieces are layered and nailed together and then caulked at the seams. In the future, these will most certainly split apart due to environmental shifts in weather and temperature. Our technology allows us to mouldings up to 48” in height and 32” in depth as a single piece.
SIMPLER AND FASTER INSTALLATION.
Returning back to the point of using nails to install wood, our composite mouldings do not require nails. Instead, they are attached to walls using an adhesive. This eliminates the need to puncture and patch holes which not only results in quicker installation times but a consistent finish too.
LIGHTER THAN PRECAST
There’s no doubt that the use of pre-cast concrete details on a structure will help create a grand vision. They are made by pouring cement into a mold or form and then left to cure.
The process from production to installation can be long and extremely costly for anyone choosing to go this route.
Mouldex Mouldings presents an alternative that will not only look identical but save time and money across the board.
SIMPLER AND FASTER INSTALLATION.
Holding a pre-cast concrete moulding in one hand and a Mouldex Moulding in the other for a comparison would be nearly impossible. You simply would not be able to lift the pre-cast. We're approximately 1/10th lighter but aesthetically, we're identical.
TIME IS OUR BEST FRIEND.
Our extrusions take much less time to produce. We are not limited by the number of moulds available. With less setup time as a consideration, we can execute thousands of linear feet per day. Our average custom production takes no longer than seven working days.
WE KNOW BUDGETS WELL.
Mouldex Mouldings are a fraction of the weight which translates into savings across the board. The extrusion process is also less labour intensive and the transportation costs to your project is a further reduction.
SIMPLIFIED INSTALLATION.
Using only an adhesive, our mouldings can be safely and securely attached to a wall without the use of any special bracing considerations. This moves the installation fairly quickly. There is also no need for cranes to set the moulding in place. Only one tradesperson is required to lift and install as our average weight is approximately 10lbs.
SUPERIOR IN APPEARANCE TO PVC/FIBERGLASS
The use of PVC/Fiberglass exterior details can be a viable solution depending on your design but it also presents limitations and drawbacks.
Mouldex Mouldings provides an array of options that will fill the voids left by PVC making it an attractive choice.
COME TOGETHER AS ONE.
PVC mouldings are made through injection which requires the use of moulds. Like wood, their selection is limited to flat and shallow profiles to save on production costs. Achieving a detailed design would have to be done by layering and nailing sections together which will eventually split due to environmental factors. Our process allows us to create any detail and any size in one piece with no seams at a much more economical price point.
PVC IS PLASTIC...
...and it looks like plastic. It fits well in certain situations such as vinyl siding exteriors but if your façade is, for example, brick, you may want to consider our mouldings that are authentic in finish and a genuine fit on any exterior.
EASIER INSTALLATION. BETTER FINISH.
Since our mouldings do not require the use of nails for installation, the final finish will be much more consistent with no holes to patch and will move ahead of your schedule.
DISOBEY THE LAWS OF EXPANSION AND CONTRACTION.
When installing PVC mouldings, consideration for expansion and contraction due to shifts in temperature must be taken into account. Manufacturers recommended leaving a 1/8” gap over 18’ spans which would then be filled with caulking. The will leave a visible seam. Mouldex Mouldings do not expand/contract and are tightly joined together. After a simple joint treatment process, the final finish coat will hide any seam.